冲击世界机电“巅峰”
写在中国水电实现世界最大单机容量机组“一年三投”之际
●创巨型水电机组首台机调试时间最短记录;
●创世界最大水电机组“一年三投”奇迹;
●填补多项次国家和世界水电机组安装空白。
中国电建水电四局2012年局史将有以上三项重要内容。
———题记
2012年12月21日17时20分,由“中国水电”实施安装的我国完全拥有自主知识产权的当今世界最大单机容量80万千瓦水轮机组——金沙江向家坝水电站6号机组(原3号机组)顺利通过72小时试运行,并网发电。加之此前11月5日、19日投产的7号机组(原2号机组)、8号机组(原1号机组),圆满实现建设方2012年“保二争三”机组预定发电目标。
历经建设者10年栉风沐雨的顽强拼搏,国家重点清洁能源工程——向家坝水电站建设实现重大工程节点目标,我国西南川滇交界处的又一颗璀璨水电明珠冉冉升起;在“中国水电”人两年多的顽强拼搏中,代表世界机电安装领先水平的电站三台机组成功并网,伴随着中国共产党十八大胜利召开,首度向外界绽放异彩。
登临高点
向家坝水电站位于四川省宜宾县和云南省富水县交界的金沙江下游河段上,是金沙江流域水电梯级开发的最后一级水电站,国家“十五”重点工程,“西电东送”中路骨干电源项目。电站整体规模仅次于三峡、溪洛渡,为我国第三大水电工程。2002年,向家坝水电站通过国家立项审核,计划2015年工程完工。
电站设计左、右岸各安装当今世界最大单机容量80万千瓦混流式水轮发电机组4台,总装机容量640万千瓦,多年平均发电量达307.47亿千瓦时。电站全部投产发电后相当每年减少原煤消耗约1400万吨、二氧化碳排放约2500万吨、二氧化氮约17万吨、二氧化硫约30万吨,是名符其实的“绿色减排”引擎,对改善四川盆地的环境质量将起到至关重要的作用。同时,随着上游梯级电站的相继建成,向家坝水电站的发电总量和电能质量也将稳定提高,电站“能源引擎”的巨大效益也将显现,巨大的电能将为华中、华东多个省市的经济社会发展注入强大的动力。
2009年,注定是世界水电机组安装史上的一个重要年份。这一年,由三峡总公司建设的溪洛渡、向家坝两电站机电安装工程开始招标。这次招标的范围包括溪洛渡水电站18台77万千瓦水轮发电机组和电站公用系统设备安装与调试;向家坝水电站8台80万千瓦水轮发电机组和电站公用系统设备安装与调试。
溪洛渡、向家坝两个电站超大型机组安装的密度之大,是世界水电史上前所未有的,具有极大的挑战性。特别是完全打着“中国制造”烙印的向家坝单机容量80万千瓦世界最大机组更是引人注目。
80万千瓦单机容量、直径19.99米的定子、直径18.97米的转子、23千伏定子额定电压、640万千瓦特高压输出,这些目前世界最高等级的技术指标,是挑战,也是荣耀。
经过百年的发展,特别是通过三峡工程,我国企业已经完全掌握了水电站机电设备制造的核心技术,成为世界先进水平的领航者,站上了世界电机制造业的“制高点”。而检验这一切成果的最终落脚点,都在机组的安装运行上。
能够承揽世界最大机组的安装施工任务,对施工企业,无疑是一个展示实力、彰显品牌的契机。
国内各路机电安装劲旅信心满满,都在摩拳擦掌。
中国水利水电第四工程局有限公司(简称:中国水电四局)走进了“逐鹿”世界最大机组安装的大军之中。
这不单是信心的体现,更是实力使然。
中国水电四局是我国为数不多较早参与电站机组安装的水电施工总承包特级企业,在过去的50多年发展历程中,先后在海内外数十座电站中承揽了144台机组安装任务,总装机接近3000万千瓦,在国内承担的机组就占到我国水电总装机容量的十分之一。
经过专家组审慎的评标议标,确定出最终的赢家。
2009年9月21日,中国水电四局接到三峡国际招标有限责任公司的中标通知书,以2.249亿元中标向家坝水电站左、右岸机电设备安装与调试工程。由此首开企业单机容量80万千瓦世界最大机组安装先河,并将“中国水电”推上了世界机电安装的“制高点”。
蓄势待发
能中标当今世界最大单机容量机组的安装施工任务,欣喜当然是有的,但更多是压力。既是前无经验可借鉴的任务,必定蕴含前所未有的挑战和困难。
能不能延续昨日的荣光,能不能创造新的辉煌?向家坝水电站成为检验中国水电四局机电安装核心竞争力的又一个舞台。
“目前世界上尚无80万千瓦特大水轮机组安装的先例,你们要抓住机遇,在施工中多搜集、多探索、多总结,整理出一套特大型水轮机组安装的经验,用于今后特大型水电站的建设。”中国长江三峡集团公司董事长曹广晶在三峡时,曾经见证了四局人“一年三投”70万千瓦机组的佳绩,也曾为四局人为三峡工程创造出3台“精品机组”而鼓掌。他对这支队伍是放心的,并寄予厚望。
“不仅要按照技术标准保证机组安装质量,而且要通过你们更加负责、更加细致的工作,力争在标准的基础上有所突破,创出精品机组。”中国水电四局的掌门人——总经理王维斌对具体负责施工的机电安装分局提出更高的要求。
这是站在企业未来发展,保持核心竞争力在市场中持续发力的一种战略考衡。
历经多年市场的洗礼,在王维斌的心中,有着更深的认识:当今机电安装市场竞争激烈,你在成长,对手也在成长。在机电安装领域,“人无我有”的时代已经过去了,要保持品牌核心竞争力,抢占市场先机,“人有我优”才是向家坝机电安装工作的核心。
这不是杞人忧天,更不是盲目自大。此时,我国自主研发的单机容量100万千瓦的机组正在紧锣密鼓筹划中,未来机电安装将在更高的一个水平上展开竞争。
而在这个核心的背后,是对施工的管理理念、组织模式、管控程序、工艺水平等等多个方面的检验。
在投标工作展开的同时,机电安装分局局长马军领已经未雨绸缪着项目的实施。一批曾经参加过三峡、拉西瓦70万千瓦机组安装的管理、技术人员名单已经落在案头;在未接到中标通知书前,项目组织机构体系已经基本清晰。
向家坝机电项目部经理的重担,毫无悬念地落在了四局机电安装分局现任党委书记李津沛肩上。曾在三峡机电项目部担任经理的中央企业劳动模范李津沛在过去工作的30年间,参加过十几座电站的机组安装,不仅在机电专业技术上出类拔萃,而且具有丰富的施工管理经验。
带着企业的重托,2009年10月20日,李津沛带着先期施工、管理、技术人员进驻向家坝电站现场,就合同要求的项目前期临建、现场勘测、设备倒运等事项展开工作。
2010年1月16日,电站主机埋件的第一个部件——8号机座环运抵电站右岸地下厂房,随即展开组装和焊接,标志着向家坝机电安装厂房标与金属结构安装工作启动。
2010年3月21日,直径14.588米、高5.48米、总重356.5吨的8号机组基础环座环一次准确吊装就位,标志着世界最大机组安装工作正式拉开序幕。
严苛标准
当前世界最大单机容量机组,在技术等级上提出了世界级的挑战。
早在向家坝机组安装之前,工程建设方就为机组安装制定出当前世界最高等级的技术要求,被称为“向家坝标准”。
此前,代表世界机组最高安装水平的是长江三峡水利枢纽单机70万千瓦机组安装标准。因国标不涉及70万千瓦特大型机组安装,该标准以国标为基础,并高于国标。
而向家坝机组安装标准在三峡标准基础上再次提升。比如,机组空气间隙为影响机组电磁不平衡的主要原因,定子与转子组装圆度、偏心及各部位半径是影响空气间隙的重要因素,国标要求空气间隙偏差为总间隙的±8%,三峡标准执行的是±6%,向家坝标准执行的空气间隙为±4%,比国标高出一倍,比三峡标准也高出近70%。
总重达1976吨、高6.3米、直径18.97米的机组转子,绝对算得上一个“庞然大物”,然而它的圆度误差控制在“向家坝标准”中仅有0.9毫米。
“当年三峡机组转子圆度控制在1.18毫米即为优良,这对直径近20米、转速低的向家坝机组转子来说,是一个极大的难关。”李津沛介绍。
从1.18毫米到0.9毫米,决定了一次世界机电安装技术水平的飞跃,标志着我国大型水轮机组安装技术首次跨入半径偏差1毫米范围。
要达到这一标准,涉及机组安装一系列复杂的程序,任何一个环节出现问题,都无法达到最终的标准的要求。
“取法乎上,仅得其中;取法乎中,仅得其下。”深谙管理之道的李津沛,对项目部的工作提出近似严苛的要求:“超越‘向家坝标准’、创建‘精品机组’。”简而言之,就是在实际工作中,将所有技术标准按照高于“向家坝标准”的标准来开展工作。如在向家坝标准中,机组空气间隙按照±4%控制,但在实际工作,按照±3%来施工,超过当年三峡标准一倍。
只有高标准,才能出精品;只有严要求,才能创精品。
为了精品目标,结合现场实际,项目部在管控模式上进行了大胆创新。
——在现场管理方面:面对工作面多、施工作业交叉的实际,为保证工效,项目将管理人员按照专业、区域划分到各班组进行管理,安排项目部和各部门主要领导夜班值班制度,保证24小时现场管理到位,形成了项目部全员管理、全过程管理和交叉、垂直管理模式。
确立“技术先行”工作制度,短时间内制定出基础埋件、转子施工措施和关键工艺控制措施,编印成册,技术人员随身携带;同时,由技术部统一分配各个专业技术干部,进入各施工班组,全程进行技术指导和控制。
推行“无边界管理理念”,鉴于各厂家提供机组安装部件存在的不同问题,为最大程度消除工期、质量阻碍,项目部提前介入,跟踪部件出厂、现场问题确认和解决复查,集业主、监理、厂家和施工四方共同参与。
——在质量管控方面:在当年较为完备的“三峡标准质量体系”的基础上,编制了更为完备的“向家坝标准质量体系”。严格控制各施工程序,在项目部专职质检人员组成的“内三检”基础上,还成立了由项目部专职质检员为初检、厂家技术人员为复检、现场监理人员为验收的“外三检”制度。
实施“转序签认”、“无缝交接”制度,项目部将各专业单元工程划分为若干个质量工序控制点,每道工序按技术要求完成后,经过“转序签认”才可以进入下一道工序,对关键工序、关键项目和关键质量重点,严格做到“无缝交接”,确保质量全程受控。
有规矩自成方圆。
短时间内,项目部在生产、质量、技术、安全上形成了符合本项目运行管理的组织架构和80余项规章、规范,为各项工作的高效开展提供了坚强的组织和制度保障体系。
创新攻坚
纵观世界上任何一座造福子孙、彪炳史册的伟大工程,都是建设者智慧和汗水的结晶。作为首次施工的世界最大水轮机组系统工程,其高技术含量不言而喻,许多难题需攻克和解决。
细节决定成败。
机组安装是一个复杂的系统工程,从埋件安装,到定子组焊吊装,再到转子组装吊装就位,牵涉上百道工序。只有每一道工序的精益求精,才能保证最后机组的正常运行。
在机组安装这样的工作中,最容易体会“细节决定成败”这句话的内涵和重要性。
在8号机转子安装中,所有的工序都围绕着转子圆度与偏心这一质量控制核心进行。
为高标准控制好转子磁轭圆度,项目部从细部着手,先后出台30多项分部技术施工规范,一个环节一个环节严格控制。
在定子组装的第一个环节定位筋安装中,189根定位筋,施工人员经过对半径、扭斜、弦长详实的计算,严格按照操作规范,最终使半径偏差控制在0.3毫米、扭斜控制在0.08毫米、弦长控制在0.2毫米以内,均超过向家坝标准,为机组日后的稳定运行打下了坚实的基础。
在转子挂磁极施工中,84个磁极本已挂完,按照厂家图纸,也满足技术要求,但为了将圆度再缩小1毫米,保证过速后机组运行更加平稳,经过大量的计算、测量、比对,施工人员最后将84个磁极的垫片全拿出来,进行减薄处理。
在转子磁轭28000余片叠片安装中,由于叠片较轻,压不住,来回跑,不易控制,施工人员每叠到300片时,便停下来测圆,把圆度调整好,再叠,如此反复进行。
严格环节控制和细致的要求,最终,8号机组转子圆度直径偏差被控制在0.64毫米,远远高于向家坝标准0.9毫米的控制规范。随后完成的7号机组圆度偏差被控制在0.79毫米,6号机组的圆度偏差被控制在0.68毫米,同样超过向家坝标准。
……
在整个机组的安装过程中,细节制胜的例子举不胜举。
项目副经理孙德召介绍,定子安装的最后一道工序是定子下线,定子有1512根线棒,分为6种类型用于不同位置的安装,这些外观看起来大致相同的线棒各自发挥着不同的作用,如果有一根安装错误,通电时就会发生出现严重的问题。而处理起来,相邻的10根线棒都要牵扯,对经济成本和时间成本都会产生巨大的影响。
还有定子耐压试验,对安装工艺也是严格的挑战,向家坝机组定子的额定电压是23千伏,为当前世界机组安装中最高电压等级,而且在耐压试验中要通过59千伏高电压的考验,因此绝缘是工艺控制的核心点之一,对部件安装工艺、清洁度都有着极高的要求,哪怕是喷错或是喷薄了油漆,都会导致严重的问题。
由于精益求精,控制得力,机组在安装过程中,各分部工程均在安装过程中未出现明显偏差,完全符合“向家坝标准”要求,主要技术指标还高于标准。
成绩还源于工艺的创新和改进。
在转子磁轭叠片安装中,施工人员发现,由于转子铁片采用激光切割技术制作,部分铁片螺孔内有加工时遗留的铁屑,磁轭铁片孔相互交错较大,螺杆在提起时容易发生卡阻现象。为避免上述隐患发生在施工现场,项目部组织人员在叠片前对每张铁片进行孔内铁屑检查处理,同时改进叠片工艺,在磁轭叠至第四紧压段时,制定特殊工艺、工装,将紧压螺杆插入磁轭孔内落到支撑上,安装紧压套筒,将上方螺母戴好后再安装下方螺母,不但控制了转子轮廓度,降低了磁轭在穿螺杆时被卡阻,还避免了磁轭凸片造成的圆度超差。
在转子热加垫这一不可逆的工序施工中,由于垫片制作要综合考虑原有各测点圆度、涨量、上下部局部刚度补偿量以及磁轭垂直度等质量指标,为保证整个过程控制准确性,技术人员将温度测量从原三圈测量增加至七圈测量。在科学谨慎的温升、温降控制中,反复多次细致测量,热加垫后的转子磁轭轮廓度从1毫米调整到最后的0.68毫米。该工序调控方案的成功,弥补了上道工序产生的偏差,质量数据完全优于“向家坝标准”。
“科学合理调整施工工序和工艺,为我们实现机组优质快速安装发挥了重要作用。”孙德召向我们举例,“在转子组装中,原工序是要对大力筋先进行调整,然后再进行磁轭叠装,在工期上会受到影响,但我们取消了大力筋的初步调整,直接进行磁轭叠装,最后进行整体调整,就极大地缩短了工期。”
还有在转子吊装过程中,项目部将转子直接落在推力头上,取消了落在制动器上的受力转换过程,既能够保证质量,又能在制动器管路未安装完成的情况下,提前实现转子吊装,更利于时间的统筹,有效地缩短了直线工期。
在过去近三年的时间里,项目部针对机组安装中出现的各种新情况和问题,先后组织组织技术人员展开了20余项技术革新和工艺调整,填补了多项国家和世界机电安装的空白,为电站整体安装工作提供强有力的技术支持。
精良的工作带来优异的成果,截至目前,项目部共完成向家坝机电安装48个单元工程,右岸水轮机埋件18个,右岸水轮机安装2个,发电机安装17个,左岸水轮机埋件11个,均被评为优质工程,优良率100%。其中右岸两台机蜗壳安装、8号机定子、转子安装被业主评为优质样板工程,左岸机电埋件安装也被业主评为优质样板工程。
承受之重
为世界最大机组安装探路奠基,为企业持续发展赢得先机。
责任激发的动力往往超出人们的预料。
招标时,建设方将向家坝8台机组安装的总体时间控制在了5年,而此前中国水电四局在三峡电站中安装了8台机组恰好用了5年。
这本身就是一个挑战。因为在相同时间里,向家坝机组要比三峡的大,理论耗时必然长,而且在向家坝机电标中还涵盖了左右岸两个独立的输电公用系统,这在四局三峡安装标中是没有的。
然而,更大的挑战还在后面。工程开工后,建设方综合考虑,对电站整体工期进行了调整,机电安装总工期被压缩至4年,而2012年原定首批两台机组发电的目标也被调整为“保二争三”。
工期缩短了,质量要求却没变。本应慢工出细活,形势陡然而变,成了又好又快,迫使项目部对原施工组织方案作出调整。
“工期一旦被确定,对我们就如同法律,必须遵守。困难再大,也要想办法克服。”李津沛说,“关键就在现场组织,按照以往正常施工肯定是赶不出的。”
为保证直线工期,安装工序多次进行调整;为激发员工潜力,一系列奖惩措施相继出台。劳动竞赛、岗位练兵、技术革新一个个活动将电站厂房安装现场沸腾在一片大干快上的热潮中。
“进点前七个半月,锥管以上机电埋件,土建要求6个月发交面,但我们第一台机5个月反交面,后面几台机都是4个月向土建反交面,为以后争取了时间。”李津沛告诉我们,“在高强度的工作压力下,广大干部职工所表现出的顽强拼搏精神,迎难而上的作风让我感动,也骄傲。”
夏季的向家坝,气温30摄氏度以上,即使什么也不干,也会汗流浃背。而在蜗壳焊接施工现场,电焊班班长安学民正带着40多名电焊工紧张作业。蜗壳材料厚度大,为保证焊接质量,必须进行不低于100摄氏度的余热。面对如此高温,所有电焊工依旧长时间保持着规范的姿势。
“预热后的钢板温度在六七十度以上,几个工人打赌,看谁能摘了手套将手放在上面10秒钟,就请他吃饭,最终谁也没赢。”安学民笑着说,“我最值得高兴的是,我们的焊接工作如期完成,经探伤检测,我们焊接的4台机组蜗壳均一次性验收合格。”
2010年,电站右岸水轮机组埋件共1094项(次)验收,合格率100%,一次验收合格率100%,全年安装工期均比合同工期提前2~3个月完成,超额完成年度计划任务。建设方用“安全、优质、高效”6个字对项目部的工作给予了充分的肯定。
第一炮打响了!
在机组安装的前两年,工期一直是项目部紧绷的“神经”之一。尤其是面对厂家到货不能满足要求这种不可控因素的影响下,就需要施工人员付出更多。
2011年,是电站7号、8号、6号机组安装的高峰期。4月,8号机组定子铁心硅钢片到货滞后,为抢工期,李津沛将项目部党员召集起来,组成“共产党员突击队”,利用晚上休息时间,与安装工一起并肩奋斗,连续一个月,最终按工期要求完成38余万张硅钢片的叠装,并一次性通过定子铁损试验。
“几台机组定子定位筋到货在不同程度上存在些问题,如果按一台一台机组来组装,因为缺陷处理,肯定要时间上要受影响,这是我们当时不能承受之重,我们就将几台机组合格的定位筋先装到8号机上,这样既保证了质量,也保证了工期。”孙德召说,“转子附件的制动闸到货时,我们发现水平度内外偏差过大,如果返厂,势必造成工期延误,我们就发动大家智慧,几个有经验的转子班老职工连续几天,昼夜在现场,运用加阶梯垫的方式进行调整,最终达到了规范要求。”
正是凭着高度的责任和严谨的工作态度,首批机组安装在困境中快速推进。到2011年下半年,项目部提前一年工期的预定目标已不存在问题。
2010年5月23日,7号机基础环和座环一次吊装就位后,项目部加紧各项安装工作。2012年2月15日,转轮吊装完成;3月31日,实现转子吊装,进入机组总装阶段;10月21日,7号机组首次启动,至11月2日进入试运行,历时13天,写下首个80万千瓦巨型水轮机组调试纪录。
2011年9月,8号机转轮吊装就位;11月6日,机组通过定子耐压试验;11月7日,通过转子耐压试验。11月12日,历时245天攻坚克难,向家坝水电站8号机组转子顺利吊装就位,电站建设进入发电倒计时。2012年3月,8号机组盘车工作结束;6月,轴承油槽注油工作完成;7月,机组总装工作结束,进入无水调试阶段;10月,机组开始充水试;11月17日进入试运行。
2011年底,6号机组定子组装工作开始。2012年5月24日,转轮顺利吊装就位;8月17日,转子成功吊装;11月,进组设备安装完毕,进入无水调试阶段;12月11日,机组首次启动,并于11日后进入试运行,创下80万千瓦巨型水轮机组调试最短时间纪录。
2011年10月,电站右岸500千伏GIS开关站、厂用电系统等电气及辅助公用系统安装工作全面展开。至2012年9月,电站右岸公用系统调试工作结束,满足首批机组投产发电条件。
与此同时,其它5台机组和公用系统安装工作也在精细化施工中快速推进。
走向巅峰
2012年11月5日,向家坝水电站首台7号机组成功发电,电力光芒为世界机电史划开了一个新的时代。
而最终“一年三投”目标的实现,更令人鼓舞。这不仅使我国80万千瓦水轮机组制作工艺得到了进一步的验证和完善,同时“中国水电”在特大机组安装领域的整装水平和雄厚实力也得到了充分的证明和彰显。
“优质、安全、高效”,本是建设方对四局人初期工作的评价,却被金沙江畔的机电人贯穿于工作始终,他们工作越干越出色,机组安装一台更比一台好。经现场检测,已投产机组其稳定性、振动、摆度、温度均超过预期控制规范,完全符合“优质”标准;施工以来,现场始终保持“零事故”状态,安全管理控制得力。而7号、8号、6号机组发电分别较合同工期提前45天、11天和97天,也真正实现了“高效”施工。
“特别是刚发电的6号机组,上下振动幅度仅有0.3毫米左右,不及一根头发丝的粗细。而机组运行状态的温度被控制在1摄氏度以内,远低于2.5摄氏度的向家坝标准,太漂亮了,太完美了!”项目总工程师赵吉鸿谈及此处,喜悦之情溢于言表。
“‘一年三投’目标的实现和机组运行的优良状况,给了我们极大的鼓舞,也更让我们坚定了在后续机组安装中创造精品的信心。”李津沛表示。
百尺竿头更进一步。铸造昨日辉煌的中国水电四局机电安装人正重整力量,以“自强不息、勇于超越”的精神,全力以赴后续机组安装施工任务,誓以更加高昂的斗志、更加踏实的作风为中国水电史乃至世界水电史树立一座高技术含量典范工程。
一场夺取世界最大单机容量机组安装全面胜利的攻坚战正在金沙江畔如火如荼进行。截至目前,电站右岸5号机组正在进行定子下线与导水机构预装已基本完成。左岸1号机组机坑交面工作已完成,定子组装工作正在加紧进行;2号机组机坑里衬和接力器基础安装工作结束;3号、4号机组蜗壳安装工作结束;公用系统1~4号机组尾水盘型阀及尾水充水前预埋管路封堵工作结束。经检验,已完各项安装工作均符合工程技术规范,为2015年全面实现电站投产发电打下了坚实的基础。
盘亘蜿蜒山道,俯遥滚滚金沙,向家坝这座凝结现代文明的水电地标已傲然雄立。高压输电银线自两岸延伸,似双翼舒展,带着民族的自豪和骄傲,正托起世界机电一个新的“巅峰”。
更多精彩内容请关注能源网-中国能源报www.cnenergy.org

- 改革开放成就中国水电走向辉煌2018 / 09 / 26
- 我国水电装机及发电量较改革开放初期增长约20余倍2018 / 09 / 26
- 巨轮远航,向海而生2018 / 09 / 17
- 历时近两年 水电技术标准“走出去”成功验收2018 / 07 / 17
- 加上成套出海标准,中国水电就无敌了2017 / 03 / 30
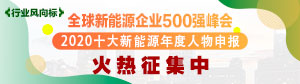
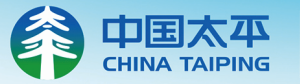
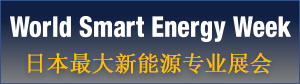
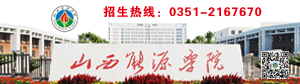
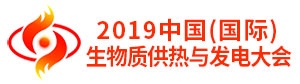
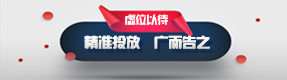
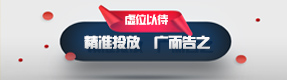
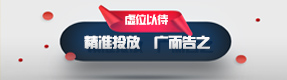
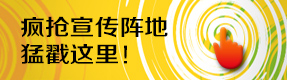
- 阳光电源日本展会签单100MW
- 国家电投年度“成绩单”亮眼
- 红沿河核电基地上网电量再创新高
- 2020清洁取暖县长论坛媒体吹...
- 国家电投首期战略论坛成功举办
- “零碳中国”倡议在京发布
- 天鼎联创携手宏华国际 共创海...
- 生态文明社会化实验室“企业...
- 中国能建参与完成的“长江三...
- 阿特斯集团2020年新春联欢会...
- 阿特斯2020全球销售大会拉开序幕
- 中国智慧能源产业联盟学术委...
- 国际新能源年会共商“转型和...
- 2020年中国水电发展论坛暨水...
- 2020年山西省能源工作会议召开
- 鉴衡成立风能专家委员会
- 2020硅藻新材料科研成果新闻...
- 能源数据与网络安全展将于3月...
- 电力网络安全形势严峻 电力关...
- 2019超临界二氧化碳循环发电...